How Robotic Inspections Can Help Increase Safety on Bridge Sites
According to a report by the American Society of Civil Engineers, there are more than 617,000 bridges across the United States, and 42% of them are a half-century old or more. Many have reached the end of their useful structural lives or are close to it. Not only are bridges aging out, but 7.5% of all the bridges across the U.S. are also considered structurally deficient, which means all or part of the bridge is unsound.
The poor condition of bridge infrastructure in many parts of the United States is making it necessary to inspect bridges more frequently to stay on the lookout for wear and damage that could cause safety issues or result in partial failure or total collapse. These inspections are critical to keep people safe and maintain the flow of traffic over important arteries, which keeps business and economic activity moving efficiently. A bridge collapse can cost people their lives and severely impact commerce in the area around it.
The inspection cycle on compromised bridges can be as frequent as once a month or more. This is a far cry from the two-year cycle that is the typical bridge industry standard.
It should be noted that bridge inspections are costly, can be dangerous, may cause further damage to a weakened structure, and can disrupt traffic.
So, what’s the alternative?
Introducing robotic bridge inspection technology.
New robotic technology supported by safe traditional tactics, like using lifts from Bridge Masters for in-person, hands-on viewing, make inspections more efficient, accurate, and safe for inspectors and drivers alike.
Robotics are particularly good for inspecting bridge stay cables and high mast light poles, two areas that can be challenging to access.
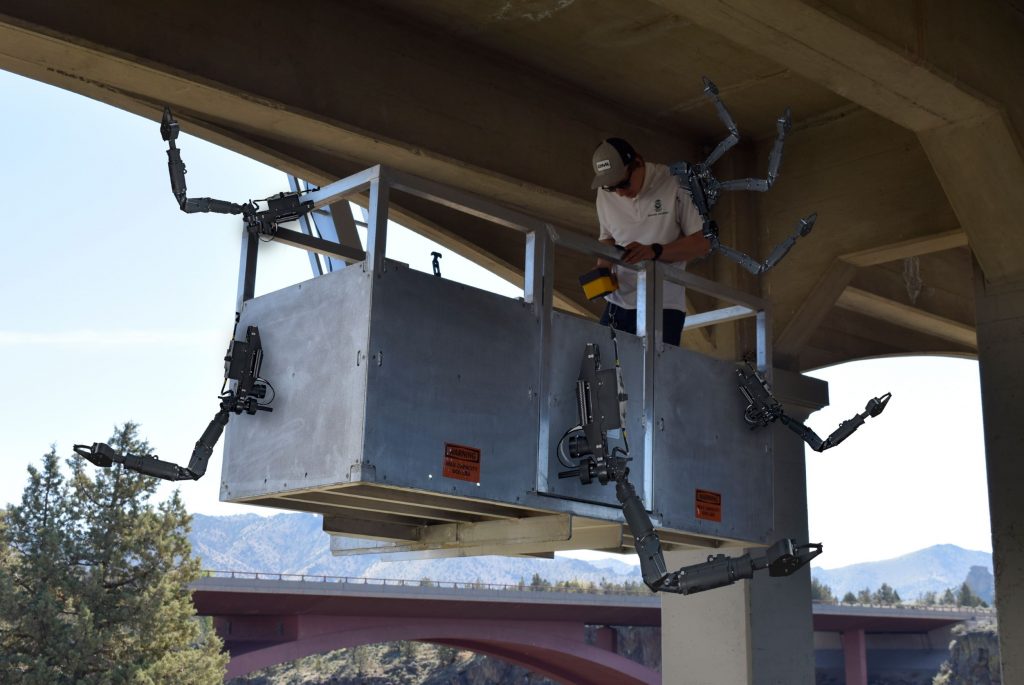
An operator demonstrates robotic arms that may be used to build robotic bridge inspection equipment in the future. Credit: RE2 Robotics, www.resquared.com
Robotic inspections of bridge stay cables.
Typically, bridge stay cables are inspected visually by experienced professionals who harness themselves to the cable. To test for structural integrity, they perform cable wedging to inspect the interior of the sheathing, looking for deterioration or corrosion of the cable stay. The four issues with this approach are:
- It’s dangerous.
- It’s costly.
- It’s often necessary to close lanes of traffic.
- Cable wedging makes it possible for water to penetrate the sheathing, which could cause corrosion or further deteriorate, or accelerate the deterioration of a cable that’s already damaged.
The latest wireless robotic nondestructive testing equipment makes it possible to do real-time inspections and evaluations of a bridge’s stay cables without putting people at risk or causing harm to the cables. The robotic equipment attaches to the exterior of the sheathing and uses technology to virtually see through it to detect and calculate loss of metallic area and look for individual broken wires within the stay cables.
Robotic equipment can inspect 100% of the stay cables and provide quantitative data, which is not possible with traditional inspection methods. When humans do the work, they can only do random sampling that provides subjective insights. Major damage might be missed if an area is not chosen for inspection. A few feet of missed bad cable could cause a calamity.
Other benefits of robotic bridge inspection technology are that it provides a real-time quantitative evaluation and delivers a permanent record of those findings. This makes it easy to support and document possible issues. It also enables you to maintain an ongoing record of inspections to track the progression of any problems that are uncovered. A data- and imagery-supported progression of decay and deterioration is far more valuable than one supported by anecdotal notes.
In addition to performing interior inspections of bridge cables, leading robotic solutions can perform 360° close visual inspections of the exterior of the sheathing, exceeding the close-visual requirements of the National Bridge Inventory, American Association of State Highway and Transportation Officials (AASHTO), and Federal Highway Administration (FHWA) for biannual inspections. On top of all this, the robots can provide full-length videos and still photographs of the entire inspection process, which can be kept as a part of your permanent inspection records.
Besides providing safer, better, and more thorough quantitative bridge inspections, causing less damage and supplying a complete permanent record of them, robotics no longer require lane closures that can slow or stop traffic.
Of course, the final decisions on the future direction of cable and other bridge repairs won’t only be based on robotic inspections. But once they indicate a problem area, climbing equipment and modern bridge lifts can be leveraged to conduct safe, in-depth, hands-on inspections and to make repairs.
Robotic high mast light pole inspections.
While not as structurally important as cables, high mast light poles help keep drivers safe. Regular inspections are critical to keep them in optimal working order.
Robotic devices can be used to conduct thorough, real-time 360° inspections of high mast lamp poles. The robot inspections exceed FHWA and AASHTO guidelines and provide permanent inspection video and photo records, enabling you to track deterioration and corrosion over time. In addition, robotics can supply a complete assessment of pole sleeves, seams, mast arms, and luminaries.
In addition to inspecting cables and high mast light poles, robotic technology is a good inspection option for other bridge-related structures, including overhead signs and other types of lighting. When it comes to inspecting lighting and signage, using robotics also eliminates the need for lane closures, which can be a bigger issue with these structures than cables. Similarly, if issues are identified by robotics, they can be looked at more closely by human inspectors using lifts and other equipment.
Finally …
According to the Federal Highway Administration, there were 842 bridge work zone fatalities in 2019 alone, the latest year that data is available. Hopefully, robot technology can help reduce this. It should also help eliminate the inconvenience and other issues related to lane closures. Finally and perhaps most importantly, when coupled with lifts and other inspection tools and equipment, robotics can help reduce the number of bridge failures and closings, along with preventing other public safety and economic issues.